The potential of digitalization in injection molding production is nowhere close to being exhausted. Nadine Despineux, Executive Vice-President Digital and Service Solutions at KraussMaffei, talks about the opportunities and solutions available to make use of the advantages of Industry 4.0 and generate measurable added value for the customer. Artificial intelligence plays a groundbreaking role here.
Interview with Nadine Despineux, Executive Vice-President Digital & Service Solutions
TEXT KraussMaffei
PHOTOS KraussMaffei
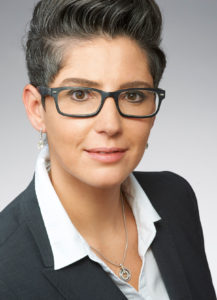
“At KraussMaffei, being customer-centered is the focus of digitalization. This approach uses individualized customer communication according to target groups or personas.”
Nadine Despineux
ahead
What impact does digitalization have on the injection molding machine industry? And how has it changed the approach to injection molding processes?
Nadine Despineux
The trend in our market is that traditional differentiating features such as price or technology alone are cited less frequently as the critical factors when buying a machine. Therefore, providers must actively look for new differentiating factors, where digitalization plays an ever larger role. The transformation from being product-centered to being customer-centered is critical here.
We have very different types of customer contact persons with diverging interests. Different target figures exist depending on whether we deal with the Head of Production, Head of Maintenance, CFO or CEO. When we take all these factors into account and develop customized digital services in conjunction with our state-of-the-art machines, we help our customers improve their business economics and market opportunities. This makes us an invaluable cooperation partner.
ahead
Can you give a concrete example from injection molding technology where these advantages of digitization and customer centricity come into play?
Nadine Despineux
The best example is our digital product socialProduction. One of the success factors is the clear focus on the customer and collaborating with them – in every stage from the initial idea to field tests to optimizing the product.
Using socialProduction, the production process of the injection molding machines is continuously monitored by a patented, self-learning process. Relevant anomalies and trends in the process are identified at an early stage based on all detected machine data and communicated proactively by means of user notifications. The process parameters are evaluated completely autonomously and without prior configuration by the process owner.
ahead
We are, after all, still in the early stages of progressing digitalization. The degree of maturity with regard to the digitalization of injection molding processes is by no means uniform yet. What solutions does KraussMaffei offer?
Nadine Despineux
You’re right in saying that the degree of maturity of digitalization within various technologies and applications is still not uniform. One challenge for our customers is for example that production facilities usually have uniform equipment because different systems are purchased from different suppliers. Therefore, the objective must be to harmonize and standardize interfaces so that systems from different manufacturers and suppliers can interact and communicate with each other.
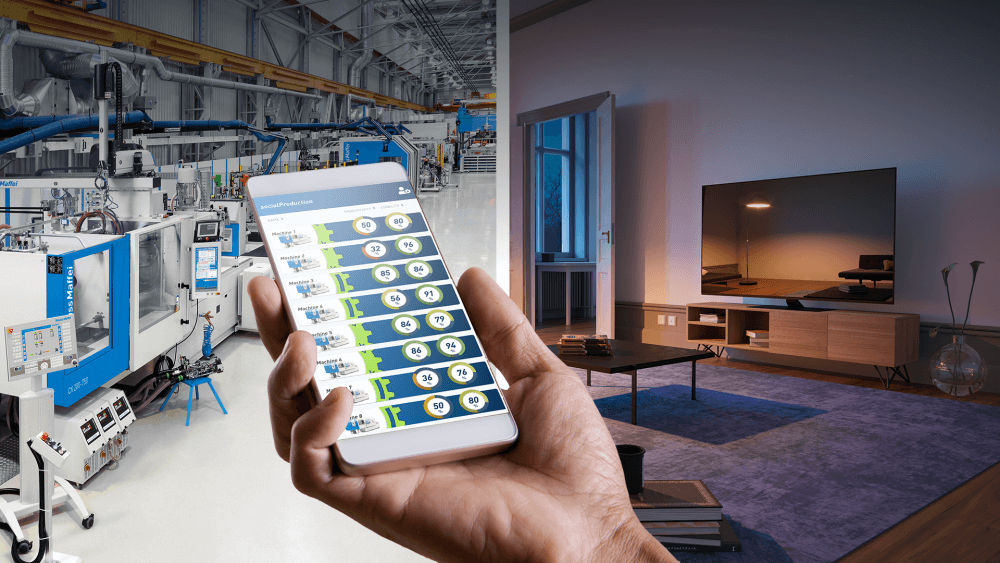
“The Euromap initiatives, which are based on OPC Unified Architecture (OPC UA), provide a state-of-the art, efficient communication standard with standards defined on a cross-manufacturer basis.”
Nadine Despineux
ahead
What doors, concretely speaking, does digitalization now open? What specific possibilities does it offer compared to the past?
Nadine Despineux
Digitalization has increased the speed at which the market is changing. At its core, KraussMaffei is a mechanical engineering company with a longstanding tradition, and so it will remain for the foreseeable future.
However, the possibilities of digitalization bring about the danger that traditional mechanical engineering companies will have to compete with tech companies from unrelated industries, namely the software and Internet industries.Therefore, we mechanical engineering companies have to combine our expertise in this domain with the expertise we have in digitalization. Today, this protects us from competition from data companies by adding more customer value than the pure software companies are able to deliver.
Digital solutions have already changed the service business in mechanical engineering, for example through remote-service solutions. Going forward, data-based solutions will also be the basis for predictive maintenance solutions. The technological prerequisites for this are already in place today.
ahead
The increasing digitalization of injection molding processes also increases the volume of data. This data contains a great deal of information that, in many cases, goes undetected at first glance. How can this information be integrated into process optimization?
Nadine Despineux
We are working to establish a closed loop for ongoing improvements to processes and products. In the first step, the purpose of the data is to enable our customers to run the machines better in order to maximize productivity and availability. Secondly, we feed the utilization data back into development in order to improve our machines.
Thirdly, the sales department benefits from the data because it understands customer needs better and can offer tailored solutions. Finally, the cycle also leads to internal process optimization here in-house – for managing technician calls, for example, or for spare parts planning.
ahead
Online support, remote service, augmented reality – these functions have already become widespread. What successes has KraussMaffei achieved in this area?
Nadine Despineux
Our digital services also follow an evolutionary process. Our simplest achievements are closely tied to the machine. This includes smartAssist, our mobile audio and video communication system with augmentation that gives the customer’s onsite service technicians access to our domain expertise and access to our experts at the global service support centers. The app can also be used with smart glasses to carry out remotely guided maintenance.
In the era of social distancing, smartAssist is exactly what our customers are looking for. Even beyond that, it reduces wait times and downtimes and saves money. Companies had more time during the lockdown to familiarize themselves with new digital tools. Plans call for smartAssist to be expanded with additional augmented reality features in the future. smartAssist is also suitable as a starter project for a co-creation process with the customer and for getting them started with digital transformation.
ahead
We are also seeing the rapid development of artificial intelligence. What role does it play for injection molding processes?
Nadine Despineux
Using intelligent algorithms, we can detect anomalies and thus potential interruptions to the process before a standstill occurs. We have developed this into our new digital product, socialProduction.
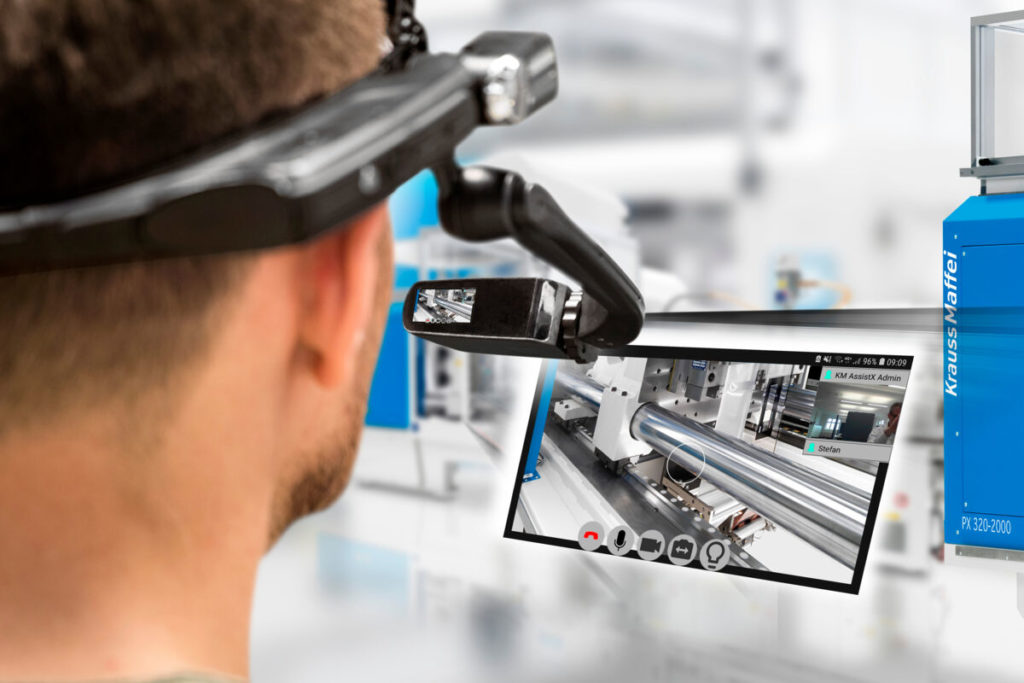
“Based on artificial intelligence technologies, a self-directed learning process monitors all available process parameters of the machine continuously.”
Nadine Despineux
KraussMaffei’s plastics process knowledge is also embedded in the algorithm. An anomaly detection system identifies anomalies in the manufacturing process at an early stage and proactively communicates this information to the user in the dedicated chat for the machine. This timely intervention prevents excess load and unnecessary wear on components or a standstill of the machine – fully autonomously, without any need for configuration.
Another customer requirement is predictive maintenance. Measuring the actual status of machine components or even predicting the expected time of failure can prevent unexpected machine downtimes. Maintenance measures are then taken only when necessary. Digital technologies enable us to record high-resolution process data that can be used to help develop mathematical models of how machine components wear.
„The mechanical and systems engineering sector has taken on a key role in reducing global greenhouse gas emissions by improving its customers’ ecological footprint with a climate-friendly portfolio of products and services.“
Nadine Despineux
ahead
Finally, let’s dare a vision for the future – What will the injection molding technology sector and the digitalisation look like in 20 to 30 years?
Nadne Despineux
The visions of Industry 4.0 and digital transformation have become reality. Customer-centricity has been a critical success factor along this journey. Standardized and modular machines, supplemented by digital solutions, enable customers to have production that is both highly efficient and flexible at the same time, all the way down to single-piece production. This is supported by a comprehensive and integrative range of services.
The mechanical engineering companies themselves will make their production climate-neutral and more local, while the machines they make will have a much wider range of application than they do today because of their automation and digitalization.
Digitalization and hyperconnectivity have enabled us to compensate successfully for the shortage of skilled workers by integrating increasingly intelligent artificial-intelligence functions into the machine, which regulate and optimize themselves. Furthermore, applications exist that both make certain workflows obsolete and permit preventive action at an early stage.