- Teaching materials manufacturer Wissner relies on recyclates and KraussMaffei
- Re-Wood®: 80 percent regional wood powder plus binder
- Re-Plastic®: 100 percent from post-consumer waste
- 80 percent export share
At the blackboard in school – the large one-meter ruler in hand: many have already had contact with the products of Wissner GmbH. The company is also a technological pioneer and has created its own recycling material, Re-Wood. It is processed on injection molding machines from the KraussMaffei CX series – with standard plasticizing.
German SMEs are family-run, think in terms of generations and are committed to sustainability. This coincides with the interests of parents. They want their children’s products to be natural, durable and, above all, safe to use. Wissner GmbH (Bensheim/Germany) combines everything: its teaching materials and games are mainly made from Re-Wood, a recycled material developed in-house. No additional trees have to be felled for it, as it is based on regional wood powder. Combined with a binder, either recycled plastic or biopolymer, Wissner brings it to granulate size and to the injection molding machines – all CX from KraussMaffei with clamping forces of 500 to 1,300 kN.
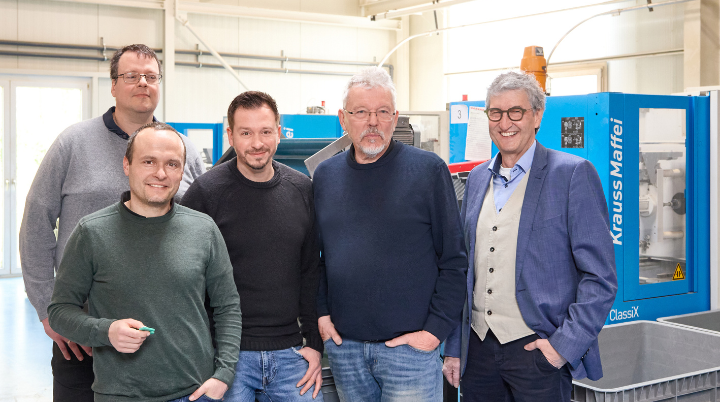
Driving forward the development of sustainable teaching and play materials together (from left): Jörn Wissner, Simon Hagemann, Jess Wissner, Jürgen Wissner (all Wissner GmbH) and Peter Meisel, Regional Sales Manager KraussMaffei
Due to its 80 percent wood content, Re-Wood has different physical properties than pure plastics. Nevertheless, it can be processed in a standard plasticizing process without any adjustments to the screw geometry or non-return valve. One thing in particular should be noted for the injection parameters: Re-Wood does not shrink – so care should be taken when reprinting.
Re-Wood products: 100 percent recyclable
Unlike real wood, Re-Wood building blocks can withstand cleaning in the dishwasher, they are very strong, almost infinitely durable and, if they do wear out, can be recycled again and again. Wissner even takes back Re-Wood products that are no longer needed. Building blocks & co. can be coated using drum coating, for example, and printing is also possible. Wissner also processes Re-Plastic®, which consists of 100 percent recycled post-consumer waste.
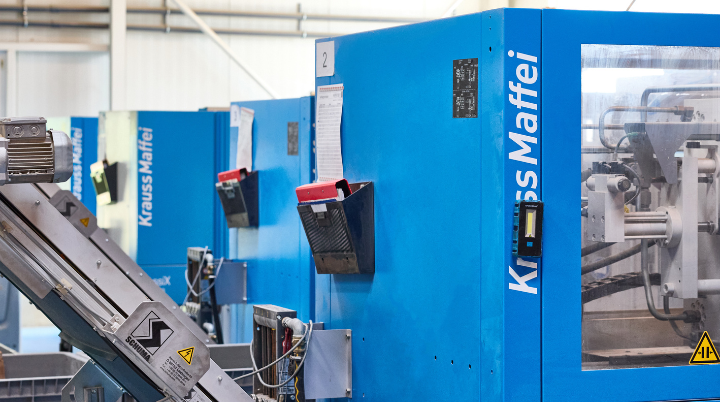
View into the production: The CX machines from KraussMaffei master the demanding processing of wood powder with standard plasticization
When the company began developing Re-Wood around ten years ago, the focus was on regional raw materials, environmentally friendly production, freedom from harmful substances and durability. It also had to be stable and saliva-proof – after all, the products are also intended for small children. Given the company’s history, combining wood and plastic was an almost logical step, as Wissner started out as a joinery in 1976, followed later by plastics processing, and in 2007 the first CX machines from KraussMaffei moved in. Around 25 employees produce items such as geometric solids, slide rules and peg cubes. The traditional focus is on teaching materials for schools and kindergartens, with the games sector becoming increasingly important.
80 per cent export share
In addition to its own products, such as the number game “Hexagon”, Wissner also offers its expertise to major players in the games industry. The industry as a whole is currently endeavoring to relocate production processes from South East Asia back to Europe. For example, the well-known Halma men are now available in Re-Wood in the special colors purple and natural. A total of 80 percent of Wissner’s turnover comes from abroad. The pricing must therefore also be attractive for less affluent regions. The efficient processing of the future material Re-Wood on the CX machines is the prerequisite for this.
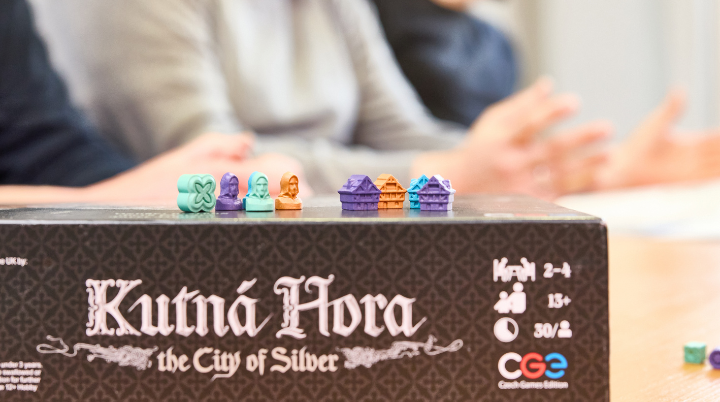
With love to details: Thanks to its excellent properties, Re-Wood is increasingly conquering the national and international world of board games
Text and photo: KraussMaffei