Separation is ‘dead’ – or very much alive?
Despite hot runner moulds, there are still countless applications where downstream separation between the usable part and the sprue is inevitable. In addition to manual separation, either sprue pickers, diverter valves, separation attachments on conveyor belts or separation drums are used. Although these are generally established technologies, there is a massive productivity potential in many companies, which often remains unused at present.
Here is an example: In the production of technical parts, two parts and one sprue are produced per shot. The cycle time is 7.5 seconds. Of this, approx. 1.5 seconds are allotted to sprue removal by means of a sprue picker. This means a theoretical productivity potential of up to 20% if the sprue separation can be installed downstream.
However, this is only realistic if the correct separation technology is used efficiently. Here, many companies are already satisfied with separation rates of 90%, although in some cases simple changes in the settings of existing equipment can further improve the quality of separation.
It depends on many parameters, which separation technology is suitable. In addition to the cycle time and the number of cavities, the geometry of the useful part and sprue plays a decisive role. For downstream separation, a certain difference in size is always necessary. In many cases this is a difference in height, but it can also be a different surface dimension.
The following list covers the main types of equipment and highlights the essential quality features.
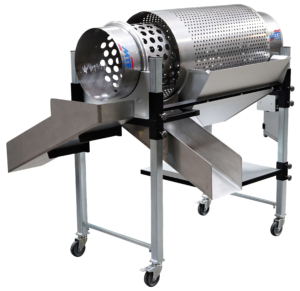
Picture: Perforated Drums
Screw Separators
For the majority of applications in the plastics industry, screw separators can be used with good results. In this case, a rotating roller with an applied screw profile is mounted above a fixed sheet metal plate. The separation gap is determined by the distance between the screw roller and the sheet metal, whereby the small parts slide underneath the screw and the large parts are pushed to the side.
In order to be able to achieve an optimum separation rate with these units, a number of design features are important. It is essential that the screw roller is stable and supported on both sides, so that the roller has the same distance to the discharge plate everywhere and does not “wobble”.
Furthermore, it is crucial that the rotational speed of the screw can be adjusted to the respective separation task. Some components require a “calm” separation process, other parts can be separated better if the screw roller rotates as fast as possible. Ideal in this context is a separate drive of the screw with integrated overload protection in order to prevent jamming of parts and to meet the requirements for optimal work safety. Thus, the speed of rotation of the auger can be controlled independently of the speed of the infeed belt. This is particularly important if, for example, the parts have to cool down first on the conveyor belt. Therefore a very slow or clocked conveyor speed and at the same time a fast rotating screw roller are necessary for an optimum separation rate. This can only be achieved with independently operating drives.
Another important detail are flexible spikes, which should be placed along the circumference of the screw and thus serve to loosen up the material to be separated. This ensures that larger pieces that have been placed in front of the screw and have blocked the passage for the smaller pieces are always set in motion, thus clearing the passage for the smaller pieces.
A flexible scraper above the screw roller prevents parts jumping over the screw during feeding – e.g. by a conveyor belt. They collide with the scraper and are thus returned to the separation process.
Separating Roller Separators and Disc Separators
Part-sprue combinations, where, for example, a flat sprue and many small parts have to be separated from each other, can usually be separated well with separating rollers or disk separators. The larger, flat sprues run over the rollers, while the small parts fall through between the rollers.
These separation techniques can therefore be used to separate parts and sprues with different surface areas.
As with the screw separators, the main focus here is on stable, double-sided support of the individual rolls and individual speed control to achieve an optimum separation result.
Furthermore, it should be possible to use different roller coverings. Depending on the task and behaviour of the parts, it may be necessary for the roller coverings to be very entraining or smooth.
Separation Drums
Separation drums are often used for larger throughput quantities or component-sprue combinations where circulation can improve the separation result. By means of the recirculation process it can be achieved that e.g. hollow part problems (i.e. the sprue lies in the component) can be solved and separated much better than with separation attachments.
There are various separation drums, depending on the difference in part geometry.
Roller Separation Drums
Roller separation drums are used to separate components and sprues with different height dimensions. They can be used for a variety of separation tasks. Here there are separation drums with individual adjustment of the separation gap or devices with a planetary central adjustment.
With individual adjustment, each roller is individually fixed in the drum cage. The distance between two rollers defines the separating gap. Since this adjustment is relatively time-consuming, such a separation drum is only suitable for applications where a machine is occupied with an article for a long time or where several similar component/sprue combinations can be separated with one adjustment.
Separating drums with central adjustment of the separating gap, on the other hand, are suitable if a wide range of products is to be separated with the aid of the drum. The central adjustment offers quick adjustment – it can be set to a new product combination within a few seconds. In this case, two rollers always form a firmly connected pair, so that only every second gap between the rollers is also a separation gap. This reduces the number of separating gaps compared to a separating drum with individual adjustment. The maximum quantity throughput is therefore lower.
With roller separation drums, it makes sense in most cases if the rollers are driven by a belt that is tensioned around the cage. This results in a counter-rotation of the rollers, which prevents jamming processes. In addition, the rotation of the rollers also increases the separation area within the drum cage. As a result, the volume throughput and also the separation rate is significantly increased compared to a drum cage with fixed bars.
Perforated Drums
Perforated drums are used when the parts to be separated do not differ in height but in their surface area (e.g. coins with different diameters but the same material thickness). The advantage of the perforated drums is on the one hand the low price and on the other hand the high throughput. Since a very small hole pitch can be chosen, the perforated drum consists almost exclusively of separation gaps, i.e. the smaller components find many opportunities to fall out of the drum per revolution.
The downside of perforated drums is that there is a fixed hole geometry and this means that the device only fits to a limited range of parts. However, complete drum cages can easily be replaced to cover a correspondingly larger spectrum of parts.
Depending on the application, many different materials can be used for the drum cages. In addition to steel and stainless steel cages, rubber or silicone materials can be used to ensure the best possible protection of parts.
Hedgehog Drums
Hedgehog drums are a special form of perforated drums. Here, sleeve tubes are applied to the outer circumference of the drum cage in extension to the holes, which have the geometry and size of the holes. This ensures that e.g. s-shaped parts cannot “wiggle” through the holes. These parts can only plunge into the sleeve tube with their tip, but then fall back into the drum cage.
In the same way, the sleeve tubes prevent sprues that are prone to snagging from getting stuck in the holes.
Rectangular Drums
Rectangular drums represent a completely independent type of separation drum. These separation drums have four separation gaps, each consisting of two 80mm wide parallel surfaces. The drum cage is completely made of stainless steel, so that these drums can also be used in the production of medical technology articles or clean room production, for example. Cleaning of the smooth surfaces is very easy.
As with the roller separation drums or screw separators, the separation is also carried out here – as with the roller separation drums or screw separators – by means of the height dimension of the components. However, the design of the separation gap parallel to the surface also prevents components from wiggling through.
The separation gap is adjusted by means of threaded spindles. The height of the separating gap can be precisely adjusted and read off by means of applied scales. This gives thus a high repeat accuracy.
Another important feature of this separating drum is the process patented by MTF Technik in which the separating gap opens with each revolution. Due to a special mechanism the separating gaps open briefly in the upper area. This allows components to be separated in rectangular drums, which would cause problems in other drums. These include, for example, very small or tapered components that can get jammed in roller separation drums. But also very soft materials (e.g. rubber or silicone) can be processed very well in this drum type.
Conclusion
Separating is far from ‘dead’. The pressure for short cycle times makes downstream separation more interesting than ever. Depending on the part spectrum, suitable and correctly adjusted separation systems can contribute to a massive increase in productivity. Investments in separation systems often pay for themselves within a few weeks.